Case Study:
How Agunsa used Eskuad to enhance equipment and machinery maintenance
Navigating the Seas of Logistics: Agunsa's Expert Shipping Operations
Agunsa is a large shipping operations company serving all of Chile as a port agent. They have been in Chile since 1960, and specialize in logistics and distribution services. They serve shipping companies, airlines, and administrate multiple ports and airports.
THE CHALLENGE
• Extreme weather
• Poor Connectivity
• Laging Operational Efficiency
• Slow Data Collection and Report Generation
• Lost data due to paper forms
• Delayed maintenance schedules
Enhancing Efficiency
Life in the field is never easy. This is especially true for natural resource companies with field teams operating in extreme conditions due to distance, climate and connectivity. All of these take a toll on operational efficiency— especially data collection and report generation.
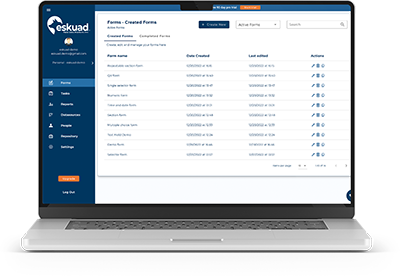
THE SOLUTION
By integrating Eskuad, a cross-platform (iOS and Android) maintenance workflow tool, companies have significantly improved their field operations. Eskuad’s features, including easy form creation, customization, instant report generation, and work order signature records, facilitate efficient workflows. Notably, digitizing maintenance processes has enhanced oversight of work order statuses, reducing machinery breakdowns and related costs.
Since implementation, benefits have extended to improved preventive maintenance, accelerated operational efficiency, better communication among teams, and easy data backup. This has led to fewer incidents, increased work order completions, and a 50% time reduction in form-filling tasks. A critical change is the shift from weekly to same-day maintenance report delivery, allowing management to promptly respond to maintenance needs with high-quality data.
50% Savings
in filling out maintenance forms
86% Decline
in waiting times for reporting updates
Savings
in detention times due to machinery failure